In
the
world
of
precision
manufacturing,
achieving
the
perfect
balance
between
quality,
performance,
and
aesthetics
is
key.
When
it
comes
to
high-gloss
sheet
metal
spinning
spare
parts,
CNC
machining
(Computer
Numerical
Control)
technology
offers
unmatched
precision
and
consistency.
Whether
you
are
producing
components
for
automotive,
aerospace,
or
high-end
consumer
products,
CNC
high-gloss
sheet
metal
spinning
ensures
the
highest
levels
of
quality,
durability,
and
visual
appeal.
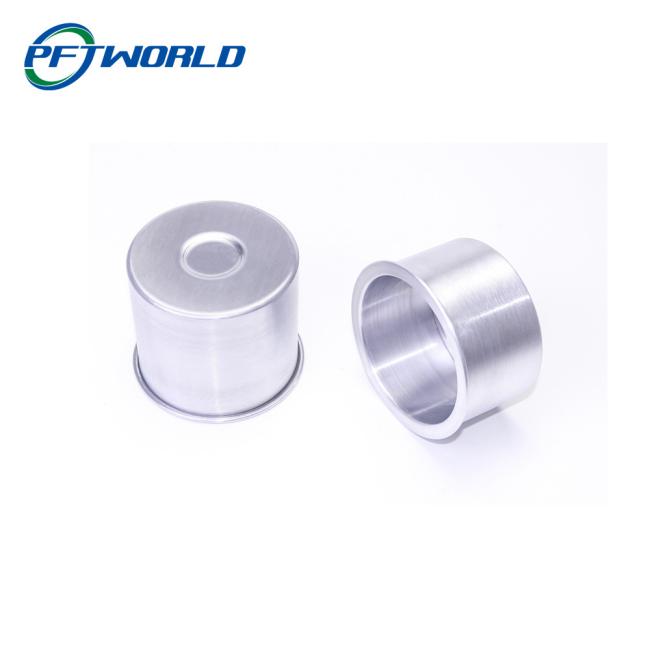
What
is
CNC
High-Gloss
Sheet
Metal
Spinning?
Sheet
metal
spinning
is
a
process
that
involves
rotating
a
metal
sheet
at
high
speeds
on
a
lathe
while
applying
force
with
a
tool
to
form
it
into
a
cylindrical
or
conical
shape.
The
key
advantage
of
CNC
spinning
over
traditional
methods
is
that
it
offers
greater
precision
and
automated
control,
allowing
for
the
creation
of
parts
with
complex
geometries
and
high-quality
surface
finishes.
When
combined
with
CNC
technology,
high-gloss
finishing
is
achieved
through
precise
adjustments
in
the
machining
process.
The
result
is
a
mirror-like
surface
finish
that
is
smooth,
shiny,
and
visually
appealing—ideal
for
applications
where
aesthetics
are
as
important
as
functionality.
Benefits
of
High-Precision
CNC
High-Gloss
Sheet
Metal
Spinning
-
Superior
Surface
Finish:
One
of
the
standout
advantages
of
CNC
high-gloss
sheet
metal
spinning
is
the
ability
to
achieve
a
high-quality,
glossy
finish.
This
finish
is
achieved
without
the
need
for
extensive
post-processing,
such
as
polishing
or
buffing,
saving
time
and
ensuring
a
consistent,
reflective
surface
across
all
parts.
-
Unmatched
Precision:
CNC
technology
offers
micron-level
precision
during
the
metal
spinning
process,
ensuring
that
your
parts
meet
exact
specifications
for
shape,
size,
and
finish.
Whether
it's
a
simple
cylindrical
part
or
a
more
complex
design
with
intricate
details,
CNC
spinning
guarantees
accuracy
and
repeatability.
-
Enhanced
Durability
and
Strength:
While
providing
an
aesthetically
pleasing
finish,
the
spinning
process
also
enhances
the
material's
strength
and
structural
integrity.
The
rotational
force
used
in
CNC
spinning
strengthens
the
metal,
making
it
more
durable
and
resistant
to
wear,
corrosion,
and
stress.
-
Flexibility
in
Design:
CNC
high-gloss
sheet
metal
spinning
is
highly
versatile
and
capable
of
producing
a
variety
of
designs,
from
simple
to
complex
shapes.
Customization
options
such
as
specific
geometries,
thicknesses,
and
dimensional
tolerances
can
be
easily
integrated
into
the
manufacturing
process,
ensuring
that
the
final
part
meets
the
unique
needs
of
your
project.
-
Cost-Effective:
CNC
spinning
is
a
cost-effective
solution
for
producing
high-quality
parts
in
both
small
batches
and
large
volumes.
The
minimal
waste
generated
during
the
spinning
process,
combined
with
the
ability
to
use
affordable
sheet
metals
such
as
aluminum
or
stainless
steel,
reduces
overall
production
costs.
-
Consistency
and
Repeatability:
Once
a
CNC
program
is
set
up,
it
ensures
consistent
quality
throughout
the
entire
production
run.
Whether
you're
ordering
one
part
or
hundreds,
CNC
high-gloss
spinning
guarantees
that
each
part
meets
the
same
exacting
standards,
ensuring
uniformity
and
reliability.
Applications
of
High-Precision
CNC
High-Gloss
Sheet
Metal
Spinning
Parts
CNC
high-gloss
sheet
metal
spinning
is
used
across
various
industries
to
produce
parts
that
require
both
functionality
and
aesthetic
appeal.
Here
are
some
key
applications:
-
Automotive
Industry:
High-gloss
sheet
metal
spinning
is
widely
used
for
producing
automotive
trim
components,
wheel
covers,
grills,
and
reflective
trim
pieces.
The
high-quality
finish
ensures
that
parts
not
only
perform
well
but
also
enhance
the
overall
appearance
of
the
vehicle.
-
Aerospace
Industry:
The
aerospace
sector
requires
parts
that
can
withstand
extreme
conditions
while
maintaining
precise
tolerances
and
lightweight
characteristics.
CNC
high-gloss
spinning
is
ideal
for
manufacturing
parts
such
as
engine
components,
aerodynamic
housings,
and
reflective
panels
that
meet
stringent
requirements
for
both
performance
and
appearance.
-
Consumer
Electronics:
Many
consumer
electronic
products,
such
as
smartphones,
laptops,
and
home
appliances,
incorporate
CNC
spun
sheet
metal
parts
with
a
high-gloss
finish.
These
parts,
including
casings,
bezels,
and
decorative
panels,
combine
both
aesthetic
appeal
and
durability.
-
Lighting
Fixtures:
High-gloss
CNC
sheet
metal
spinning
is
widely
used
for
producing
lighting
fixtures,
lamp
housings,
and
reflectors
that
require
a
polished,
smooth
surface
to
optimize
light
reflection
and
appearance.
The
high-gloss
finish
ensures
both
functionality
and
an
attractive
design.
-
Medical
Equipment:
Medical
devices
often
require
precision-made
parts
with
a
polished,
easy-to-clean
surface.
CNC
high-gloss
sheet
metal
spinning
is
used
to
create
components
like
enclosures,
mounting
plates,
and
protective
covers
that
meet
the
strict
standards
for
safety,
hygiene,
and
reliability.
-
Architectural
Applications:
From
decorative
metal
panels
to
architectural
accents,
CNC
high-gloss
sheet
metal
spinning
is
used
to
create
eye-catching
designs
that
are
both
strong
and
visually
striking,
making
it
perfect
for
use
in
facades,
column
covers,
and
interior
elements.
|
CNC
Turning,
CNC
Milling,
Laser
Cutting,
Bending,
Spining,
Wire
Cutting,
Stamping,
Electric
Discharge
Machining
(EDM),
Injection
Molding,3D
Printing,Rapid
Prototype,Moulds
etc.
|
|
Aluminum:
2000
series,
6000
series,
7075,
5052,
etc.
|
Stainlesss
steel:
SUS303,
SUS304,
SS316,
SS316L,
17-4PH,
etc.
|
Steel:
1214L/1215/1045/4140/SCM440/40CrMo,
etc.
|
Brass:
260,
C360,
H59,
H60,
H62,
H63,
H65,
H68,
H70,
Bronze,
Copper
|
Titanium:
Grade
F1-F5
|
Plastic:
Acetal/POM/PA/Nylon/PC/PMMA/PVC/PU/Acrylic/ABS/PTFE/PEEK
etc.
|
|
Anodized,
Bead
Blasted,
Silk
Screen,
PVD
Plating,
Zinc/Nickl/Chrome/Titanium
Plating,
Brushing,
Painting,
Powder
Coated,
Passivation,
Electrophoresis,
Electro
Polishing,
Knurl,
Laser/Etch/Engrave
etc.
|
|
±0.002
~
±0.005mm
|
|
Min
Ra
0.1~3.2
|
CERTIFICATE
|
ISO9001:2015,AS9100D,ISO13485:2016,ISO45001:2018,IATF16949:2016,ISO14001:2015,ROSH,CE
etc.
|
FAQ
1.
Are
you
a
manufacturer
or
a
trading
company?
We
are
a
factory
located
in
Shenzhen,
China,
with
20
years
of
rich
experience,
covering
6000
square
meters.
Complete
facilities,
including
3D
quality
inspection
equipment,
ERP
system
and
40
machines.
If
necessary,
we
can
provide
you
with
material
certificates,
sample
quality
inspection
and
other
reports.
2.
How
to
get
a
quote?
Detailed
drawings
(PDF/STEP/IGS/DWG...),
including
quality,
delivery
date,
materials,
quality,
quantity,
surface
treatment
and
other
information.
3.
Can
I
get
a
quotation
without
drawings?
Can
your
engineering
team
draw
for
my
creativity?
Of
course,
we
are
also
glad
to
receive
your
samples,
pictures
or
detailed
size
drafts
for
accurate
quotation.
4.
Can
you
provide
samples
before
mass
production?
Of
course,
the
sample
fee
is
necessary.
If
possible,
it
will
be
returned
during
mass
production.
5.
What
is
the
delivery
date?
Generally,
the
sample
lasts
for
1-2
weeks
and
the
batch
production
lasts
for
3-4
weeks.
6.
How
do
you
control
quality?
(1)
Material
Inspection
-
Check
material
surfaces
and
approximate
dimensions.
(2)
First
inspection
of
production
-
ensure
critical
dimensions
in
mass
production.
(3)
Sampling
inspection
-
check
the
quality
before
delivery
to
the
warehouse.
(4)
Preshipment
inspection
-
100%
inspection
by
QC
assistant
before
shipment.
7.
After
sales
service
team
If
you
have
any
problems
after
receiving
the
product,
you
can
provide
feedback
through
voice
call,
video
conference,
email,
etc.
within
one
month.
Our
team
will
provide
you
with
solutions
within
a
week.