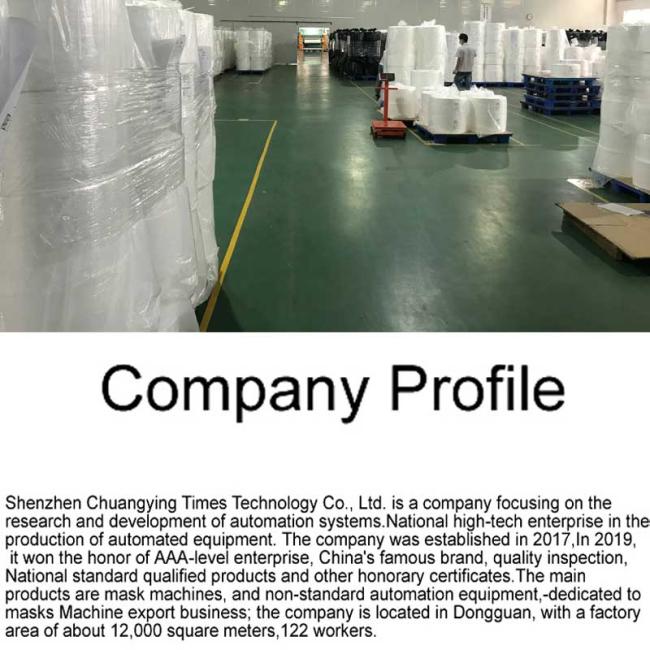
Q:
How
long
is
the
delivery
time?
Answer:
The
general
situation
is
3-5
days
for
delivery.
If
you
need
a
customized
mask
shape,
it
will
take
7-10
days.
Please
refer
to
customer
service
for
details.
Question:
The
machine
I
want
is
too
inconsistent
with
what
you
showed
on
the
Internet.
Can
I
do
it?
Answer:
Yes,
you
need
to
provide
machine
pictures
and
finished
mask
pictures.
Question:
What
should
I
do
if
I
buy
a
machine
and
I
won’t
install
it
back?
Answer:
South
Korea
and
Vietnam
have
after-sales
and
can
be
installed
on
site.
Other
countries
can
send
installation
videos
and
remote
video
guidance.
Many
foreign
customers
install
this
way.
You
only
need
to
install
the
four
screws
of
the
connector
of
the
filming
machine
and
the
earband
machine,
learn
to
load
the
cloth
and
operate
normally.
The
company
will
be
equipped
with
text
version
and
video
version
of
the
whole
teaching.
Q:
How
long
is
the
warranty
period?
Answer:
The
warranty
period
is
one
year.
The
ultrasound
is
three
months.
During
the
warranty
period,
the
parts
are
damaged
and
the
company
provides
new
parts.
The
following
information
comes
from
the
Internet
for
reference
only
In
the
process
of
equipment
testing
of
the
melt
blown
cloth
production
line,
the
reasons
that
affect
the
thickness
and
thinness
of
the
melt
blown
cloth
were
analyzed,
and
the
following
treatment
methods
were
proposed
for
customers'
reference.
Reason
analysis:
The
melt
blown
cloth
molds
are
all
single-row
spinneret
holes.
If
the
holes
are
blocked
in
some
positions,
the
process
is
abnormal,
and
the
melt
pressure
is
not
uniform,
the
weight
will
be
uneven,
and
the
hardness
will
be
different.
Here
we
focus
on
the
melting
and
plasticizing
temperature.
The
principle
of
"from
low
to
high"
should
be
followed
from
the
blanking
to
the
plasticizing
section
to
ensure
that
the
material
is
gradually
melted
and
plasticized,
and
the
temperature
should
not
be
too
high
or
too
low.
A
high
temperature
will
reduce
the
fiber.
The
strength
of
the
fabric
makes
the
cloth
brittle,
poor
in
hand,
and
poor
in
plasticization
if
the
temperature
is
too
low,
the
viscosity
of
the
solution
is
high,
the
thread
is
not
thin
enough,
the
softness
is
not
enough,
and
the
hand
feels
hard.
Process
issues
are
not
discussed
here.
Different
models
have
different
response
methods.
The
process
ratio
is
determined
according
to
the
quality
of
the
fabric
on
site,
that
is
to
say,
the
quality
of
the
melt
blown
cloth
determines
the
ratio
of
process
parameters.
The
hot
air
volume
and
pressure
in
the
machine
debugging
process
also
have
a
great
relationship.
The
selection
of
meltblown
equipment
accessories
should
match
the
host.
Solution:
1.
Use
an
acupuncture
needle
0.2-0.25
smaller
than
the
spinneret
hole
to
accurately
pass
the
hole
to
the
position
to
clear
the
blockage
of
the
melt
channel.
There
are
many
cleaning
methods,
so
choose
the
best
cleaning
method.
2.
Generally,
the
melt
blown
die
head
can
adjust
the
air
knife.
By
adjusting
the
air
knife
and
the
air
volume,
the
distribution
of
the
fiber
filaments
can
be
balanced.
3.
Since
the
melt
blown
die
head
is
generally
electrically
heated,
it
is
divided
into
several
specialties.
The
heating
unit
can
be
controlled
separately,
and
the
heating
unit
can
be
adjusted
separately
to
locally
adjust
the
melt
pressure
and
melt
viscosity
for
optimization.
4.
The
fiber
spreading
can
also
be
adjusted
by
adjusting
the
uniformity
of
the
lower
suction
through
the
lower
suction
baffle.
Generally,
if
the
cloth
surface
is
soft,
the
fiber
fineness
is
good,
and
the
filtration
rate
is
high,
but
the
corresponding
resistance
will
be
relatively
high.
Melt-blown
mask
filter
materials
are
used
as
functional
fabrics.
The
main
measurement
standard
is
not
the
test
data.
As
long
as
the
data
meets
the
standard,
the
hardness
and
softness
will
not
have
a
big
impact.
The
meltblown
die
head
is
the
core
component
of
the
meltblown
cloth
production
line.
As
one
of
the
current
scarce
materials,
the
production
and
supply
of
masks
have
attracted
much
attention.
Due
to
the
large
demand,
the
current
global
market
is
in
short
supply
of
high-quality
meltblown
cloth.
To
solve
the
epidemic
prevention
and
control
period
As
for
the
shortage
of
medical
masks,
Yastar
started
the
research
and
development
of
meltblown
cloth
molds.
After
two
weeks
of
data
collection,
meltblown
process
analysis,
mold
design
demonstration,
mold
processing
technology
testing
and
other
preliminary
work,
the
team
successfully
developed
650,
800,
1200,
1600.
,
2400mm
national
standard
coat
hanger
meltblown
cloth
die
head.